Comprehensive Insights into Industry 4.0 and Industrial IoT Advancements
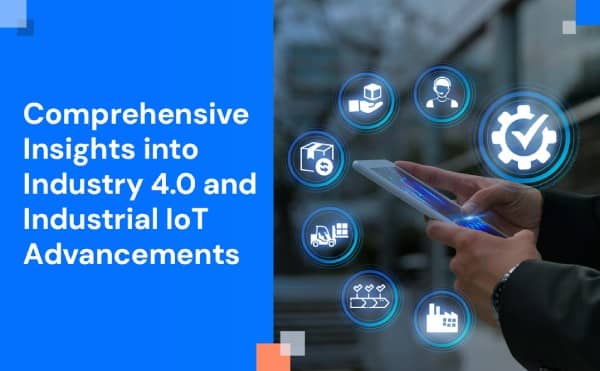
Introduction
Welcome to our comprehensive guide delving into Industry 4.0 and the Industrial Internet of Things (IIoT). In this thorough exploration, we unravel the evolution of manufacturing across the different industrial revolutions and the pivotal role played by the core pillars of Industry 4.0. From the inception of machinery to the integration of advanced technologies like IoT, automation, and predictive analytics, join us on this journey through the revolutionary advancements shaping the future of manufacturing.
History of Industrial Revolution
The First Industrial Revolution, from the late 1700s to early 1800s, introduced machinery like the power loom and spinning jenny, replacing manual labor with steam-powered equipment.
The Second Industrial Revolution, from the late 1800s to the early 1900s, saw rapid technological growth, including electricity, telephones, steel, and the advent of assembly lines for interchangeable parts.
The Third Industrial Revolution, in the latter 20th century, embraced digital electronics with microprocessors, PCs, cellphones, and the Internet, launching the Information Age.
The Fourth Industrial Revolution, our current era, emphasizes automation, machine-to-machine communication, IoT, intelligent factories, predictive maintenance through machine data and AI, and additive manufacturing, reducing human involvement in some processes.
Core Pillars of Industry 4.0 Transformation
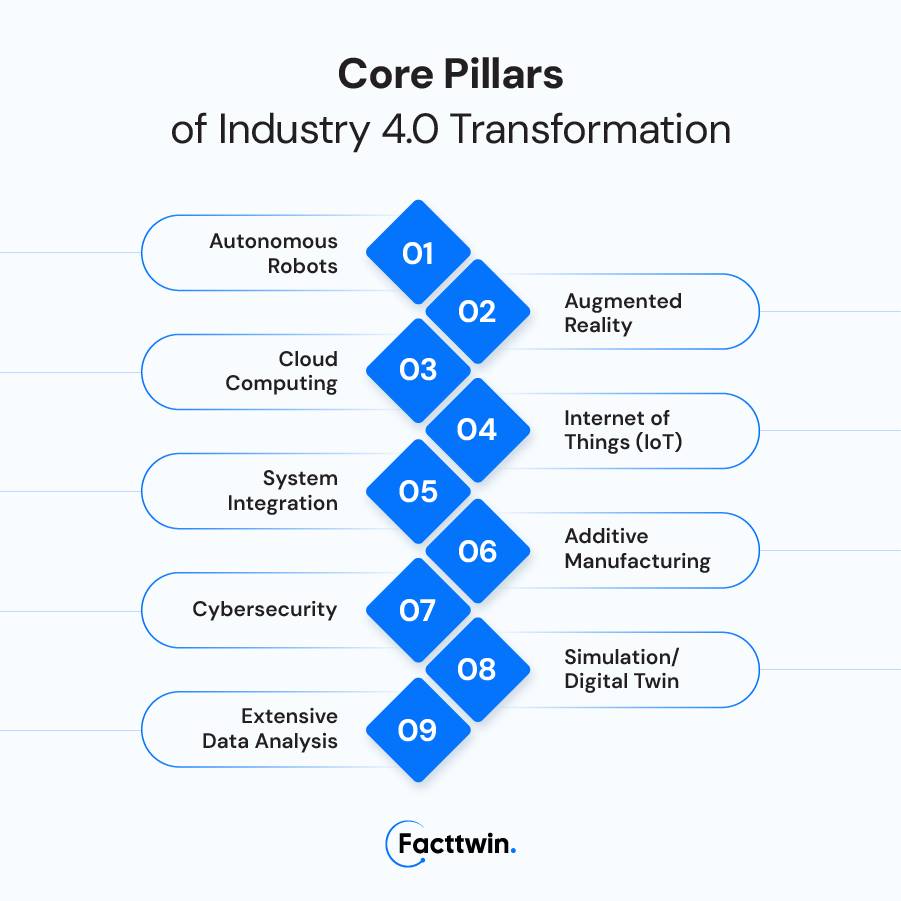
Industry 4.0, a transformative era in manufacturing, rests on several core pillars that redefine production processes. Its nine pillars encompass interconnected technologies like IoT, automation, data analytics, and additive manufacturing, driving the evolution towards intelligent factories and decentralized decision-making.
Autonomous Robots
They are self-operating machines that perform tasks without human intervention, enhancing efficiency in manufacturing and logistics.
Augmented Reality
AR overlays digital information onto the physical world, aiding in training, maintenance, and real-time data visualization.
Cloud Computing
Cloud Computing provides scalable and on-demand access to shared resources and data storage, facilitating connectivity and collaboration across systems.
Internet of Things (IoT)
Interconnect devices enable the gathering and exchanging of data, optimizing processes, predictive maintenance, and resource management.
System Integration
Seamlessly connects various technologies and processes to streamline operations and enhance efficiency.
Additive Manufacturing
A manufacturing that constructs objects layer by layer using 3D printing, enabling rapid prototyping and customization while reducing material waste.
Cybersecurity
Ensures protection against cyber threats and vulnerabilities in interconnected systems and data networks.
Simulation/ Digital Twin
Virtual replication of physical systems enabling real-time monitoring, analysis, and predictive capabilities for optimizing performance and decision-making without impacting the actual entity.
Extensive Data Analysis
Involves processing and interpreting large volumes of data to derive insights for informed decision-making and process improvement.
Industry 4.0 and Industrial IoT (IIoT)
Industry 4.0 and IIoT come from older ideas but have changed to fit new improvements. The Industrial Internet of Things is about connecting machines and devices used in industries, like factories or manufacturing, to the Internet so they can share data and communicate. This helps make processes more efficient, monitor equipment, and improve productivity in industrial settings.
Using IIoT in Industry 4.0
At the core of Industry 4.0 initiatives lies the integration of IoT technologies. A prominent application involves innovative factory approaches, where interconnected sensors and equipment exchange data, enabling real-time improvements. Advanced AI, powered by machine learning, autonomously refines workflows by learning from historical and anticipated patterns, minimizing delays and streamlining operations. These represent the many paths through which IIoT drives innovation, reshaping operational norms across various facilities.
Key Component & Technology in Industrial IoT
The complexity of IoT, a disruptive technology, isn’t surprising. Even in its basic form, a successful implementation demands the coordination of numerous technical and non-technical components.
Hardware
IoT Endpoints or Sensors / Actuators
IoT endpoints, called sensors or actuators, encompass hardware or software designed to detect changes or trigger actions. These components generate data that can be analyzed at the endpoint, gateway, or platform levels. Enterprises utilize IoT endpoints in various operational assets like manufacturing equipment, jet turbines, and office spaces.
IoT Edge Platform or Gateway
IoT endpoints connect to gateways that manage data transmission and control. These gateways act as intermediaries between multiple endpoints, offering enhanced device autonomy, management, and scalability compared to direct edge-to-cloud methods. They effectively handle diverse endpoints from different vendors.
Software
IoT platform
Data from IoT sensors, collected via IoT endpoints and gateways, is routed to a centralized IoT platform hub. This hub plays a pivotal role in provisioning, managing, and analyzing IoT devices, integrating backend systems, and enabling data analytics. Most commonly, these hubs are cloud-based Platforms as a Service (PaaS), although some providers offer them as on-premises software or both, combining IoT-specific and general-purpose application platform capabilities for seamless functionality.
User Interface
A user-friendly UI is an accessible layer for end-users to access information effortlessly without added complexity. These applications aim to present IoT data in the most straightforward way possible.
Existing Enterprise Software
In early IoT implementation, the focus often neglects user interface development, with more emphasis placed on device integration and selecting IoT platforms. However, the significant impact of these projects on existing enterprise applications is often underestimated.
A successful IoT solution requires seamless integration with enterprise applications, spanning core systems like ERP, CRM, MES, BMS, SaaS, mobile apps for asset monitoring, and legacy technologies. This integration optimizes core business processes and maximizes the benefits of IoT technology.
Impact of Industrial IoT Advancements on Modern Manufacturing
In manufacturing, the Industrial IoT (IIoT) signifies a natural progression of automation and connectivity, dominating global IoT spending.
Industrial IoT offers improved operational efficiencies and innovative business models for businesses dealing with physical goods. It expands automation, asset management, customer service enhancements, and revenue generation possibilities.
Companies facing intense competition with disruptive technologies heavily invest in IIoT to enhance growth and amplify productivity. Across industries like manufacturing, oil and gas, and mining, IIoT holds immense potential to boost productivity and streamline operating costs.
In manufacturing, IoT fosters more innovative environments by enhancing visibility and aiding companies in optimizing operations and readiness for future demand. These solutions empower employees to access pertinent information and applications via mobile devices, ensuring remote accessibility anytime, anywhere.
The advantages of Industrial IoT are described as follows:
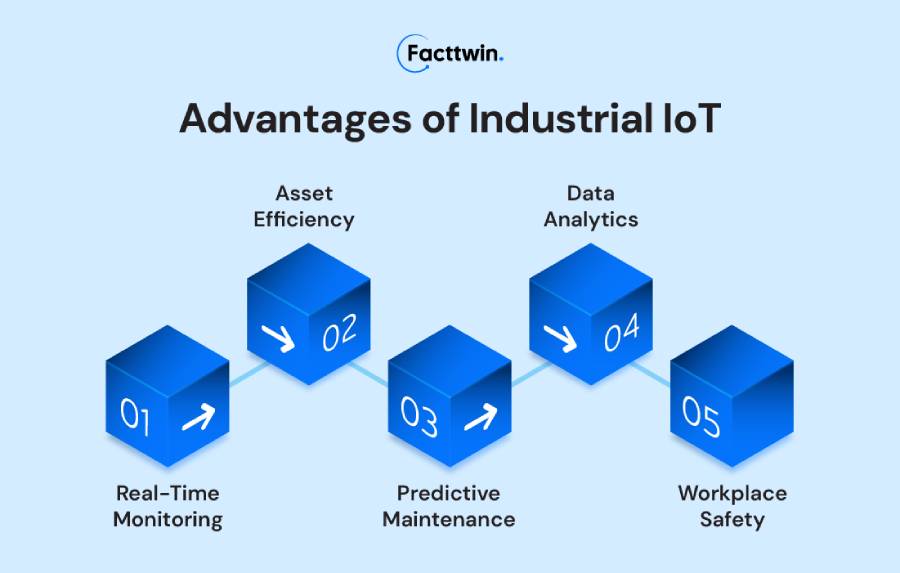
Real-Time Monitoring
Industrial IoT enhances visibility and control for manufacturing plants, remote units, and supplier factories, ensuring real-time monitoring for optimized asset utilization.
Asset Efficiency
Implementing IIoT allows asset performance tracking, predicting failures, and boosting operational efficiency.
Predictive Maintenance
IIoT aids in monitoring equipment health, scheduling maintenance based on usage, and executing effective preventive measures, reducing unplanned downtime.
Data Analytics
IIoT integrates machine-to-machine communication with data analytics, enabling OEMs to analyze machine data for better predictive models.
Workplace Safety
IIoT prioritizes workplace safety, minimizing injuries and optimizing operational efficiency.
Challenges in Industry 4.0 and Industrial IoT
Cost Challenges in IIoT Implementation
Implementing Industrial IoT (IIoT) incurs substantial expenses in development, support, and skilled resources, often posing difficulties in justifying costs without clear ROI expectations.
Connectivity Challenges
Legacy devices’ lack of connectivity hampers data collection and analysis in IIoT, exacerbated by the rapid growth of connected devices surpassing network coverage, necessitating scalable IoT networks for effective deployment.
Security Risks
Expanding attack surfaces in IIoT demand stringent cybersecurity measures to safeguard against breaches that compromise data and potentially disrupt manufacturing operations, requiring continuous endpoint testing and vulnerability mitigation.
Complexities in Data Analysis
Despite the abundance of sensors and analysis tools, harnessing insights from voluminous IIoT data remains challenging, necessitating skilled data scientists for effective data utilization and informed decision-making.
Skills Gap Impacting IIoT Adoption
The evolving landscape of IIoT underscores the need for a skilled workforce, yet a shortage of qualified personnel hampers various aspects of IIoT, including design, deployment, and maintenance, impeding overall adoption efforts.
Facttwin – Industrial IoT Platform
Facttwin revolutionizes manufacturing with universal machine connectivity, empowering your production with real-time analytics and unwavering data integrity, all from a single dashboard. At Facttwin, we envision a future where factories are no longer just places of production but ecosystems of efficiency, intelligence, and sustainability.
Smart Factory – Unleash Real-Time Operational Insights
Facttwin’s Smart Factory solution introduces a new era of value addition, revolutionizing manufacturing operations. With its real-time insights and advanced analytics, this solution enables seamless data collection and empowers proactive decision-making. It enhances operational efficiency by offering comprehensive machine insights, real-time batch efficiency analysis, and precision quality control. Moreover, its proactive alerts and universal compatibility in reporting empower decision-makers with valuable, location-independent insights, optimizing processes and driving operational excellence.
Discover more about these featureshere.
Machine Health Monitoring- Maximize Machine Uptime
Machine health monitoring revolutionizes operational efficiency, adding significant value to your operations. Advanced data capturing provides profound insights into machine health, guiding precise and informed decision-making. The intuitive Maintenance Head Dashboard ensures swift oversight and action, leveraging real-time machine status updates for proactive maintenance strategies. With real-time oversight and precision monitoring, irregularities are swiftly identified, supported by a proactive alert system that forewarns potential anomalies. Comprehensive fault analysis and trend analysis empower predictive maintenance, optimizing machine performance and ensuring uninterrupted operations. Accessible machine health insights drive proactive decision-making, fostering a culture of robust maintenance and elevating overall operational excellence.
Industry 4.0 – FAQ’s
What is Industry 4.0 artificial intelligence?
Industry 4.0 leverages artificial intelligence (AI) to optimize manufacturing processes through predictive analytics, autonomous systems, and machine learning.
Is Industry 4.0 the same as IoT?
Industry 4.0 encompasses IoT as a crucial component but extends beyond it, focusing on the integration of various technologies to drive smart manufacturing.
Which industries are using Industrial IoT?
Industries like manufacturing, oil and gas, healthcare, transportation, and agriculture are actively adopting Industrial Internet of Things (IIoT) solutions.
What are the benefits of Industry 4.0 in IoT?
Industry 4.0 enhances IoT by enabling predictive maintenance, optimizing processes, improving efficiency, and facilitating data-driven decision-making.
What is the Industry 4.0 concept?
Industry 4.0 refers to the fourth industrial revolution, emphasizing automation, connectivity, and data exchange in manufacturing technologies.
What is Industry 4.0 for dummies?
Industry 4.0, in simple terms, represents the integration of digital technologies in manufacturing to create smart, connected, and efficient production systems.
What does Industry 4.0 focus on?
Industry 4.0 focuses on smart manufacturing, leveraging technologies like IoT, AI, robotics, and big data to optimize production processes and systems.
What are the Industry 4.0 standards?
There are various standards evolving for Industry 4.0, including interoperability, security, and connectivity standards like OPC UA, RAMI, and TSN.
What is the difference between IoT and IIoT?
IoT encompasses a wide range of connected devices, while IIoT specifically focuses on industrial applications, such as manufacturing and infrastructure.
What is an example of IIoT?
An example of IIoT is predictive maintenance in manufacturing, where sensors collect machine data to predict equipment failures and prevent downtime.
What are the benefits of IIoT?
IIoT offers benefits like increased operational efficiency, predictive maintenance, reduced downtime, better asset utilization, and data-driven decision-making.
What is the key technology of IIoT?
Key technologies of IIoT include sensors, connectivity solutions, edge computing, cloud platforms, and advanced analytics enabling data-driven insights.
Conclusion
In conclusion, Industry 4.0 and Industrial IoT are cornerstones of the manufacturing landscape. The journey from steam-powered machines to real-time data analytics has transformed factories into hubs of intelligence and efficiency. With the integration of IoT, predictive maintenance, and data-driven strategies, manufacturing is poised for unprecedented productivity and operational excellence. Embracing these advancements opens doors to a future where factories transcend mere production, evolving into centers of innovation and sustainability.