A Guide to Quality Control (QC) in Manufacturing
Embarking on the manufacturing journey is like setting sail on a quest for perfection. Imagine Quality Control (QC) as your trusty navigator, ensuring that every piece crafted is top-notch.
This guide is your treasure map to understand QC in manufacturing. It’s not about complex theories; it’s about practical strategies and smart techniques that makers like you use to create stuff that’s just spot-on.
From setting standards to embracing advanced methods, let’s take a stroll through the world of QC, where precision meets passion, and quality isn’t just a checkbox – it’s a promise to make things awesome.
Ready for the journey? Let’s dive in!
What is Quality Control in Manufacturing?
Quality control in manufacturing is a systematic process to ensure the product meets all the set standards. Fulfilling customer expectations also comes under the criteria of quality check. It involves thorough inspection, testing, and monitoring of the production process. Quality control in product management is very important, especially if you are competitive with bigger players in the market.
It identifies and rectifies defects or deviations from established quality criteria. The overarching objective is maintaining high consistency, reliability, and performance in manufactured goods. Ultimately, it helps enhance customer satisfaction and ensure the reliability of the end products.
Quality Control Methods and Techniques
When it comes to quality control in production management, it is crucial to follow quality control methods. Here are some of the techniques that you can follow.
Inspection
In manufacturing, inspection is like giving things a close look – checking raw materials, parts, and finished products to make sure they meet our standards.
Testing
In testing, we put products through different tests – like checking if they work right. Also, you can measure things and identify how they react to chemicals or electricity.
Statistical Process Control (SPC)
Statistical Process Control is a bit like having a watchful eye on the processes. We use numbers and stats to ensure everything runs smoothly and to catch surprises.
Process Control Techniques
Process Control Techniques are about managing how we make things. We tweak and adjust our methods to avoid mistakes and improve our quality.
Quality Assurance
Quality Assurance is like planning to keep things top-notch. We set up rules and measures to make sure our products are consistently good from start to finish.
Apart from methods and techniques, there are some quality control measures as well, which you have to take care of. Make sure to make a balance between all of them.
Why Is QC Needed?
Industrial Quality control (QC) is important in various ways. It plays a major role in industrial manufacturing for several reasons:
- Customer Satisfaction
- Compliance
- Cost Reduction
- Brand Reputation
- Risk Mitigation
- Operational Efficiency
We will discuss these points in detail later in the section on why QC is important. Now, let’s discuss the six industrial quality control techniques you can implement.
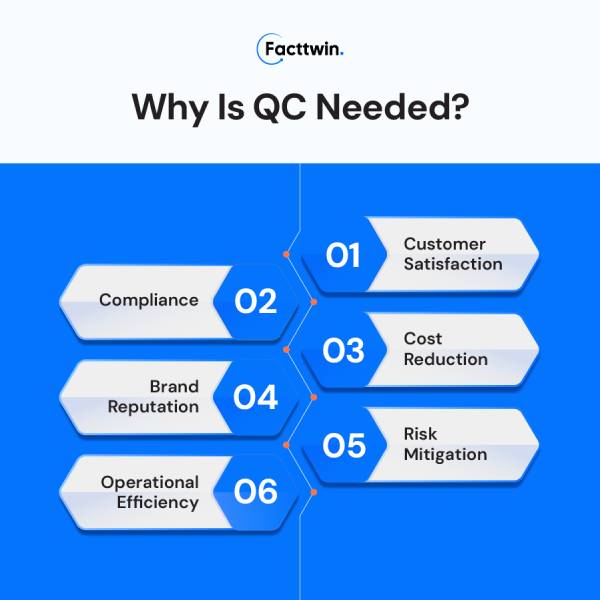
6 Industrial Quality Control Techniques in Manufacturing you can Use
Are you curious about how manufacturing experts keep a close eye on quality? Let’s dive into six powerful quality control techniques that can make a real difference in ensuring top-notch products.
Statistical Process Control (SPC)
Think of it as the guardian angel of production. SPC uses smart statistical tricks to monitor the manufacturing process constantly. It spots trends, variations, and possible issues, ensuring everything runs smoothly within set limits.
Six Sigma
Imagine a superhero for minimizing defects – that’s Six Sigma. This methodology doesn’t just aim for good; it goes for perfection. Using statistical analysis and clever problem-solving, Six Sigma ensures a high level of consistency in processes and products.
Pareto Analysis
Ever wonder how experts prioritize what needs fixing first? Enter Pareto Analysis. It’s like a wise friend who points out the big stuff. This technique identifies and ranks the most significant factors causing defects or quality problems, helping teams focus on what truly matters for effective industrial quality control.
Root Cause Analysis (RCA)
Think of RCA as a detective story for manufacturing glitches. It’s a systematic process of digging deep to discover why defects happen. By addressing the root causes, manufacturers fix the immediate issue and prevent it from reappearing.
Failure Mode and Effect Analysis (FMEA)
FMEA is like having a crystal ball for potential problems. This technique looks into the future, assessing what could go wrong in a process or product. Ranking possible failures based on severity, occurrence, and detectability helps teams address issues before they consider impacting quality.
Control Charts
If you want a visual storyteller for your manufacturing process, think of Control Charts. They’re like graphs that show how things change over time. These charts help maintain stability in the production process and signal when something needs attention.
These techniques aren’t just jargon – they’re the secret weapons that manufacturing pros use to keep quality in check and products at their very best. Now, let’s unfold the mystery behind these quality control tactics.
The Importance of Quality Control in Manufacturing
Ever wondered why quality control is the unsung hero in manufacturing? Let’s unfold the story behind its paramount importance, driven by reasons that resonate with the heart of every successful business.
Customer Satisfaction
Picture this – meeting or surpassing what customers expect is like hitting the bullseye. Quality control ensures our products consistently match the high standards set, creating lasting smiles and building lasting trust.
Brand Reputation
Think of brand reputation as a priceless treasure. Delivering reliable, top-notch goods builds a positive image like a magnet for new customers and a comforting hug for the ones who stick around.
Compliance and Regulations
Navigating through rules can be tricky, but quality control is our guide. It helps us stick to the script, following stringent regulations and standards. This avoids legal troubles and penalties and keeps our reputation sparkling clean.
Cost Reduction
Fixing things early is like being a financial wizard. Quality control identifies and solves issues in the production line pronto, reducing waste and cutting down the overall cost of not-so-great quality. It’s efficiency at its finest.
Risk Mitigation
Imagine quality control as our superhero cape against risks. It minimizes the chances of product recalls, unhappy customers, and warranty claims. This superhero move is vital for keeping our financial health in top shape.
Operational Efficiency
Think of quality control as the conductor of our manufacturing orchestra. It makes sure every instrument plays in harmony. Identifying improvement areas, optimizing workflows, and reducing disruptions keep our operations singing sweet tunes.
Competitive Advantage
In the global marketplace, being a standout is gold. Delivering high-quality products isn’t just a feature; it’s a game-changer. It attracts customers who value reliability and performance, setting us apart.
Continuous Improvement
Quality control is our compass for the journey of improvement. It’s not just about catching defects; it’s about a mindset – a culture of always getting better. Regular monitoring and tweaking lead to a manufacturing process that evolves and improves over time.
Benefits of Using Quality Control in Manufacturing
Implementing quality control in manufacturing offers many benefits that positively impact the business and its products. Here are some of the big benefits of quality control in manufacturing.
Consistent Product Quality Control
Product Quality control ensures that products consistently meet or exceed specified standards. This consistency enhances customer satisfaction and loyalty.
Cost Savings
By identifying and rectifying defects early, quality control reduces the need for rework, scrap, and warranty claims. This saves costs and improves overall operational efficiency.
Enhanced Customer Satisfaction
High-quality products result in satisfied customers. It is important to meet customer expectations to build trust and enhance the company’s reputation. It ultimately leads to repeat business and positive word-of-mouth recommendations.
Compliance with Standards
Quality control helps manufacturers comply with industry regulations, standards, and legal requirements. This is very crucial when it comes to avoiding legal issues and regulatory fines.
Increased Efficiency
Monitoring and controlling manufacturing processes matter a lot. It helps in increasing efficiency in a significant way. This includes identifying and eliminating bottlenecks and optimizing workflows to decrease production downtime.
Competitive Advantage
Offering superior quality products gives a competitive edge in the marketplace. Customers often prefer products with a reputation for reliability and performance.
Risk Mitigation
QC helps identify and mitigate risks associated with product defects. Proactively measuring all the criteria makes it easy to prevent potential issues. Through this, it also becomes easy to protect the company’s financial stability.
Reduced Customer Complaints
High-quality products result in fewer defects, which reduces customer complaints. This preserves customer relationships and saves time and resources spent on addressing issues.
How to Implement Quality Control in Manufacturing
Implementing quality control in manufacturing requires a well-thought-out and strategic game plan. Here’s your guide through the key steps to make sure your products consistently shine with quality:
Define Quality Standards
Let’s start by setting the bar. Clearly define what quality means for your products. This involves laying out internal standards and considering industry regulations or customer expectations.
Establish Quality Control Policies
Next up, create the rulebook. Develop comprehensive quality control policies that leave no stone unturned. These policies should spell out the procedures, responsibilities, and expectations at every stage of the manufacturing process.
Train Personnel
Time to get everyone on the same page. Provide thorough training for your production team. Ensure they understand the importance of quality control, their specific roles, and the procedures like the back of their hands.
Set Up Inspection Points
Think of it as placing checkpoints along the way. Identify crucial points in your manufacturing process where inspections can take place. This includes checking raw materials and various stages of production.
Select Appropriate Testing Methods
Choosing the right tools for the job is crucial. Select testing methods and equipment that perfectly match the characteristics and requirements of your products. This could involve visual inspections, precise measurements, and various testing techniques.
Implement Statistical Process Control (SPC)
Let’s get a bit tech-savvy. Bring in statistical process control methods to keep a watchful eye on the manufacturing process. This helps spot trends, variations, and areas that could use a bit of fine-tuning.
Document Procedures
Paperwork matters. Document all your quality control procedures and ensure they’re easy for your team to access. This documentation should cover everything from inspection criteria to testing methods and procedures for corrective actions.
Implement Corrective and Preventive Actions
When things go off course, have a plan. Develop a system to address non-conformities. Implement corrective actions to tackle immediate issues and preventive actions to ensure they don’t reoccur.
Supplier Quality Management
Extend the quality control umbrella to your suppliers. Set criteria for incoming materials and conduct audits to ensure their processes align with your gold quality standard.
Invest in Technology
Let’s make things smoother. Consider investing in automated inspection systems or quality management software. These technological boosts can streamline processes and take the accuracy of your quality control to the next level.
How does Facttwin Software can help with Manufacturing Quality Control?
Facttwin’s cutting-edge software plays a pivotal role in manufacturing quality control, offering robust solutions that elevate product excellence. Here’s how Facttwin makes a difference:
Machine Health Monitoring
Facttwin’s machine health monitoring product ensures the heartbeat of your machinery stays strong. By constantly analyzing machine data, it detects anomalies and potential issues in real-time, allowing for proactive intervention. This minimizes unexpected downtime and contributes to consistent product quality by maintaining the optimal performance of critical equipment.
Smart Factory Integration
Facttwin’s smart factory solution transforms traditional manufacturing into a seamless, intelligent process. It enables comprehensive control and monitoring by interconnecting machinery, processes, and data. This integration fosters efficiency by identifying bottlenecks and optimizing workflows, directly impacting the quality control process. Real-time insights into the entire production ecosystem empower manufacturers to make informed decisions, ensuring every product meets the highest standards.
Ready to transform your manufacturing process and ensure quality control. Contact us for more details.