Digital Twins: History, Examples, & Gaining Insights
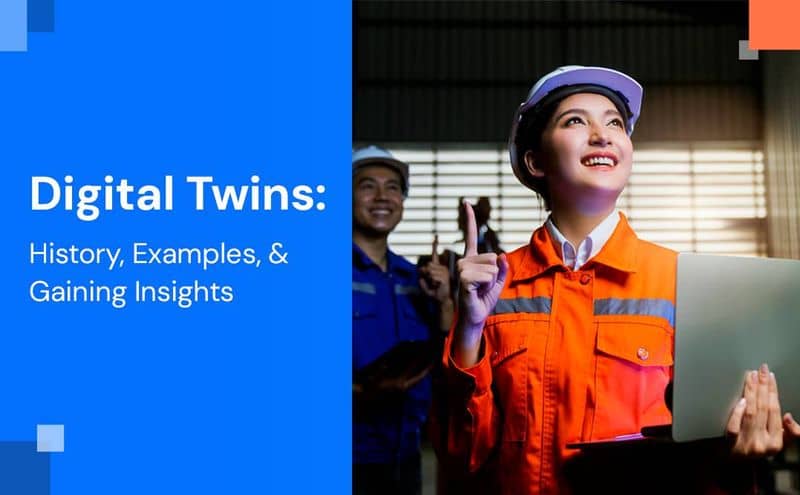
Introduction
Digital twins, with their potential to bring agility and resilience to operations, are gaining significant attention. Their value is evident among CEOs.
McKinsey research indicates that 70% of C-suite technology executives
at large enterprises are already exploring and investing in digital twins.
Let’s dive into the basics of digital twins, the complexity surrounding digital-twin technology, and learn about the different types of digital twins and where you can find them in various industries.
What is Digital Twin Technology?
A virtual counterpart of a physical object makes it as simple as that. We’ll explore more about this beyond just objects later in the blog. This technology simulates the behavior, performance, and characteristics of a physical counterpart in virtual
space. Various industries, including manufacturing, healthcare, and transportation, can apply it to optimize processes, predict maintenance needs, and enhance overall efficiency.
Digital Twin Evolution: History & Significance
The idea of digital twins began with early computer-aided design (CAD) systems in the 1960s and 1970s, allowing engineers to create digital models for design. NASA used similar digital models for space exploration in the 1980s. The term “digital twin”
gained prominence in the early 2000s, and with the rise of the Internet of Things (IoT) and Industry 4.0 in the 2010s, this technology evolved further.
Today, they are widely used across industries like manufacturing and healthcare, connecting digital models with real-world data for simulations, predictions, and optimizations. As technology continues to advance, digital twins are becoming crucial
in managing complex systems.
Digital Twin Examples: Real-world Applications
Explore how digital twin technology can be applied across industries with these examples:
Manufacturing Efficiency
It is used in manufacturing to replicate and monitor production processes in real-time. This helps optimize operations, predict maintenance needs, and enhance overall efficiency.
Healthcare Simulation
In healthcare, this technology simulates organs or biological systems, aiding in medical research, surgical planning, and personalized treatment approaches.
Urban Planning
Virtual twin model and manage city infrastructure, such as transportation systems and energy grids, enabling efficient resource allocation and enhancing urban resilience.
Aerospace Engineering
The aerospace industry utilizes the twin technology to replicate and analyze aircraft components’ performance, predicting maintenance needs and optimizing fuel efficiency.
IoT Device Testing
To create virtual replicas of Internet of Things (IoT) devices, allowing for testing and analysis before physical implementation to ensure reliability and functionality.
Energy Infrastructure Optimization
In the energy sector, this model optimizes the performance of power plants and renewable energy infrastructure, maximizing efficiency and minimizing environmental impact.
The Benefits of Digital Twin Technology in Industries
Virtual twin offers a range of benefits across industries, enhancing efficiency and decision-making. Here are the key advantages:
Optimized Operations
Real-time monitoring and analysis of processes enable enhanced operational efficiency, increased productivity, and minimized downtime.
Predictive Maintenance
Simulating the performance of physical assets allows for accurate prediction of maintenance needs, ensuring timely repairs and minimizing unexpected breakdowns.
Improved Product Design
In product development, virtual counterparts aid in prototyping and testing, enabling more informed design decisions and reducing the time-to-market for new products.
Enhanced Decision-Making
Comprehensive views of assets or processes empower decision-makers with accurate and real-time data for informed and strategic decision-making.
Resource Optimization
In sectors like energy and manufacturing, virtual counterparts assist in optimizing resource usage, leading to cost savings and a more sustainable approach to operations.
Increased Safety
Analyzing potential risks and scenarios in a virtual environment contributes to the development of safer working conditions and products.
Personalized Healthcare
In healthcare, virtual counterparts support personalized medicine by simulating individual patients’ physiological responses, aiding in treatment planning and drug development.
Environmental Sustainability
Contributing to sustainability efforts, virtual counterparts optimize processes, reduce waste, and enhance energy efficiency in various industries.
Remote Monitoring and Control
The ability to remotely monitor and control assets or processes is particularly valuable in situations where physical presence may be challenging or risky.
Continuous Improvement
Facilitating continuous improvement, virtual counterparts provide insights into performance over time, allowing organizations to refine processes and adapt to changing conditions.
Digital Twin Use Cases: Practical Applications Across Sectors
Digital twins find application in various industries, revolutionizing processes and decision-making. Here are some notable use cases:
Manufacturing
Optimizing manufacturing processes involves providing real-time insights into production lines, enabling predictive maintenance, and enhancing overall efficiency.
Healthcare
In healthcare, simulations of patient profiles aid in treatment planning, drug development, and personalized medicine. They also support surgical planning and medical research.
Smart Cities
Modeling and managing urban infrastructure contribute to optimizing city planning, transportation systems, and energy grids for improved resource allocation and sustainability.
Aerospace
The aerospace industry utilizes simulations to analyze aircraft components, predict maintenance needs, optimize fuel efficiency, and ensure safety in flight operations.
Energy Management
Modeling and optimizing the performance of power plants, renewable energy sources, and distribution networks contribute to efficient energy production and reduced environmental impact.
Internet of Things (IoT)
Facilitating the testing and analysis of IoT devices before physical implementation ensures reliability and functionality in connected systems.
Automotive Design
Utilized in the automotive industry for virtual testing and prototyping, leading to improved vehicle design, safety, and performance.
Supply Chain Optimization
Replicating supply chain processes enables organizations to optimize logistics, reduce lead times, and enhance overall supply chain efficiency.
Building Design and Management
In architecture and construction, simulations assist in designing and managing buildings, predicting energy consumption, and optimizing space utilization.
Water Management
Simulations of water distribution systems help manage water resources efficiently, detect leaks, and ensure the sustainability of water supply networks.
Types of Digital Twin
Product Twins:
- Description: Represents physical products or assets in a digital space.
- Application: Used in product design, testing, and optimization.
Process Twins:
Description: Models and simulates manufacturing or operational processes, integrating data into a centralized dashboard for real-time monitoring and analysis. Application: Enhances efficiency, monitors workflows, and optimizes processes through comprehensive
insights.
System Twins:
- Description: Models and simulates manufacturing or operational processes, integrating data into a centralized dashboard for real-time monitoring and analysis.
- Application: Enhances efficiency, monitors workflows, and optimizes processes through comprehensive insights.
Asset Twins:
- Description: Focuses on individual assets, such as machinery or equipment.
- Application: Enables predictive maintenance, monitors performance, and extends asset lifespan.
Digital Thread:
- Description: Connects and integrates data throughout a product’s lifecycle.
- Application: Ensures a seamless flow of information from design to manufacturing and beyond.
Performance Twins:
- Description: Analyzes and simulates the performance of processes or assets.
- Application: Provides insights for optimization and continuous improvement.
Spatial Twins:
- Description: Creates a digital replica of physical spaces, such as buildings or cities.
- Application: Used in urban planning, construction, and facility management.
Human Twins:
- Description: Models human characteristics, behaviors, and interactions.
- Application: Applied in healthcare for personalized treatment plans and ergonomic design.
Digital Business Twins:
- Description: Represents digital aspects of an organization, including processes and data.
- Application: Aids in digital transformation, business process optimization, and strategic planning.
Supply Chain Twins:
- Description: Models and optimizes supply chain processes.
- Application: Enhances logistics, reduces lead times, and improves overall supply chain efficiency.
Digital Twin in Manufacturing: Revolutionizing Production Processes
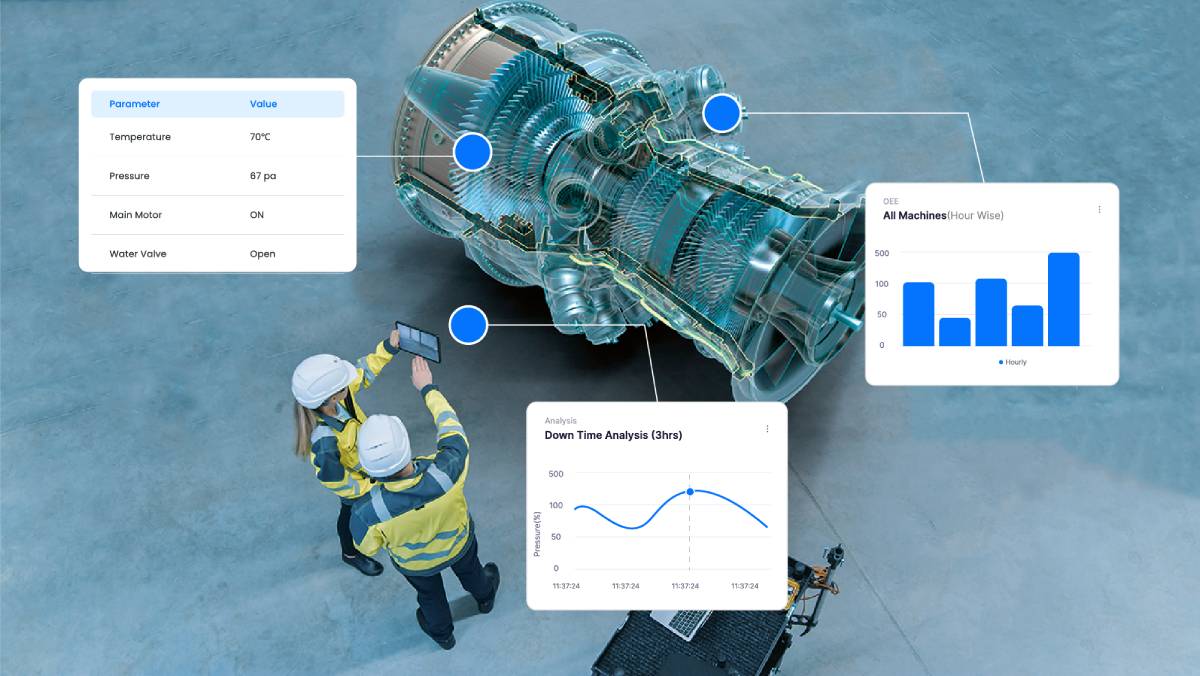
Digital twins have revolutionized the manufacturing industry by providing a dynamic and data-driven approach to design, production, and maintenance processes. Here’s how they are reshaping manufacturing:
Product Design and Prototyping
They enable manufacturers to create virtual prototypes of products, allowing for detailed analysis and testing before physical production. This reduces the need for extensive physical prototypes and accelerates the design process.
Process Optimization
By modeling and simulating manufacturing processes, digital twins help optimize production workflows. Manufacturers can identify bottlenecks, streamline operations, and enhance overall efficiency, leading to cost savings and improved productivity.
Predictive Maintenance
They facilitate predictive maintenance of machinery and equipment. By continuously monitoring the performance of assets in real-time, manufacturers can anticipate maintenance needs, minimize downtime, and extend the lifespan of equipment.
Quality Control
Real-time monitoring of product quality during the manufacturing process is enabled by digital twins. Any deviations or defects can be identified early, allowing for immediate adjustments to maintain high-quality standards.
Supply Chain Integration
Manufacturers use them to model and optimize the entire supply chain, from raw materials to finished products. This integration enhances visibility, reduces lead times, and improves coordination between different stages of production.
Resource Efficiency
They help in managing and optimizing resource usage, including energy, materials, and labor. This contributes to sustainable manufacturing practices by minimizing waste and reducing environmental impact.
Customization and Personalization
With digital twins, manufacturers can cater to individual customer needs through customized and personalized production. This flexibility allows for the efficient production of small batches or even individualized products.
Real-Time Monitoring and Control
Manufacturers gain real-time insights into the status of machinery, production lines, and overall plant operations through digital twins. This visibility enables proactive decision-making and rapid responses to changing conditions.
FAQs: Exploring Digital Twin Technology
What is a Digital Twin?
A digital twin is a virtual model of a physical entity, integrating real-world data to simulate its behavior in a digital environment.
How Does Digital Twin Technology Work?
It involves gathering data from sensors on physical objects to create dynamic virtual models that reflect real-time performance and assist in decision-making.
What Are the Main Benefits of Digital Twins?
Key benefits include optimized operations, predictive maintenance, improved product design, enhanced decision-making, and increased safety and sustainability.
Which Industries Benefit Most from Digital Twins?
They are particularly beneficial in manufacturing, healthcare, aerospace, urban planning, and energy management.
How Do Digital Twins Contribute to Environmental Sustainability?
By optimizing processes and reducing waste, digital twins help industries adopt more sustainable practices.
What Role Do Digital Twins Play in Healthcare?
In healthcare, they are used for simulating biological systems for research, surgical planning, and personalized treatment.
What is the Difference Between a Digital Twin and a CAD Model?
Unlike a static CAD model, a digital twin is dynamic, continuously updating with real-time data to provide an interactive and comprehensive representation.
Conclusion
In conclusion, digital twin technology stands as a transformative force, reshaping industries by creating virtual replicas of physical entities. From a history rooted in early design systems to versatile applications across manufacturing, healthcare,
and beyond, digital twins offer dynamic solutions. Their diverse types, ranging from product and process twins to spatial and human twins, showcase adaptability. In manufacturing, digital twins optimize processes, enable predictive maintenance,
and drive efficiency. The journey into the basics of digital twins reveals a paradigm shift with far-reaching implications for innovation, sustainability, and operational excellence across diverse sectors.