A Comprehensive Guide to Overall Equipment Effectiveness (OEE) in Manufacturing
When it comes to industrial production, understanding and optimizing the efficiency of equipment is paramount for success.
Today, we will discuss everything about Overall Equipment Effectiveness. Its pivotal metric evaluates the performance of machinery by considering Availability, Performance, and Quality.
Apart from this, we will also explore its significance, calculation methods, common pitfalls, and the transformative benefits it brings to manufacturing processes.
What Is OEE (Overall Equipment Effectiveness)?
Overall Equipment Effectiveness (OEE) is a pivotal performance metric in manufacturing. It smartly evaluates how efficiently equipment is utilized. It encompasses three critical factors:
- Availability
- Performance, and
- Quality
OEE enables organizations to pinpoint areas for improvement by appropriately evaluating the machinery. It also optimizes production processes and enhances overall operational efficiency.
Now, the next question comes to how OEE is used.
It’s pretty much clear that organizations use OEE to assess and improve operational performance by identifying and addressing inefficiencies. It offers practical insights into –
- How efficiently equipment is used
- The duration of downtime and
- Issues related to the quality of production
Manufacturers use OEE data to make informed decisions and streamline processes. As a result, you get increased profitability and competitiveness in the market.
What Are the Six Big Losses When It Comes to Overall Equipment Effectiveness (OEE)?
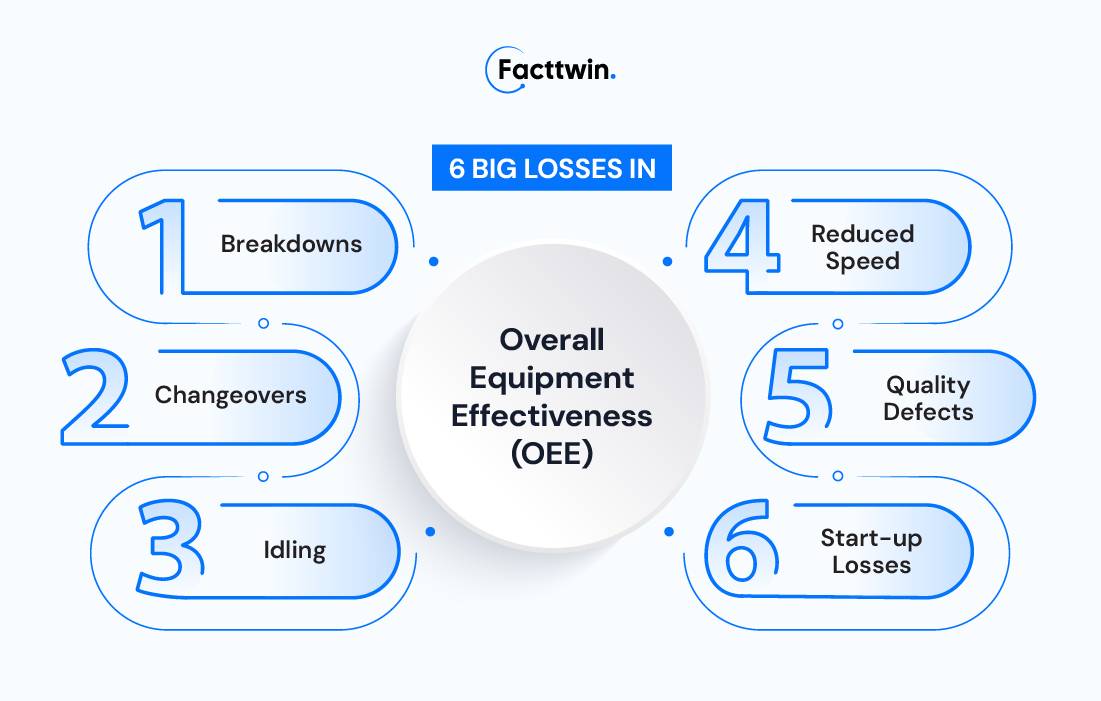
The Six Big Losses in the context of Overall Equipment Effectiveness (OEE) represent significant factors that contribute to inefficiencies and reduced productivity in manufacturing processes:
- Breakdowns:Unplanned equipment stoppages that result in downtime and hinder continuous production.
- Changeovers:Time-consuming transitions between different products or setups, causing delays and reducing overall operational efficiency.
- Idling:Instances when equipment is not in operation, often due to material shortages, waiting for instructions, or other non-production-related reasons.
- Reduced Speed:Instances where machinery operates slower than its optimal capacity diminish overall output.
- Quality Defects:Production of defective or substandard products, necessitating rework and affecting the overall quality of the output.
- Start-up Losses:Delays and inefficiencies occur during the initial phases of equipment start-up, leading to decreased production during those periods.
Five Benefits of Using Overall Equipment Effectiveness (OEE) to Improve Production
Five Perks of Incorporating Overall Equipment Effectiveness (OEE) into manufacturing operations extend a bouquet of advantages, elevating production standards and operational finesse:
- Boosted Productivity:OEE acts as a compass, guiding organizations to spot and rectify inefficiencies. This proactive approach trims downtime and fine-tunes production processes, which increases overall productivity. Machinery hums along more smoothly and effectively.
- Downtime Dwindles:With a systematic eye on the Six Big Losses, OEE plays the role of a guardian, curbing unexpected downtime. The result? A seamless, uninterrupted production flow ensures that equipment remains in action for a more significant chunk of time.
- Elevated Product Quality:OEE spreads its wings over the quality facet of manufacturing, acting as a vigilant guardian against defects. By zeroing in on quality metrics, organizations sculpt a higher standard for their products.
- Resource Harmony:OEE unfolds insights into the marriage of resources—equipment and labor—within the production process. This orchestration results in resource allocation. It ultimately improved efficiency and cost savings.
- Smart Decision-Making:OEE metrics provide invaluable data for decision-makers. Armed with a holistic grasp of equipment performance, organizations make decisions that are not just educated but also visionary. From maintenance schedules to production planning and continuous improvement initiatives, a culture of data-driven decision-making takes root. These collective benefits weave a narrative of a manufacturing environment that is not just competitive but also agile.
How do you calculate OEE (Overall Equipment Effectiveness)?
Calculating Overall Equipment Effectiveness (OEE) involves combining three key metrics—Availability, Performance, and Quality. The formula is as follows:
OEE=Availability×Performance×Quality
This formula doesn’t just crunch numbers; it paints a panoramic view of how equipment flexes its muscles. It shows crucial elements like machine uptime, speed, and the creation of quality products. It’s the compass guiding manufacturing prowess toward the north star of optimal efficiency.
Simple OEE Calculations:
Assessing equipment efficiency doesn’t have to be complicated. Simple OEE calculations use basic metrics to check availability, performance, and quality. It’s a straightforward way to get an initial sense of overall equipment effectiveness.
Preferred OEE Calculation:
When it comes to figuring out how well the equipment is doing, the preferred OEE calculation takes a closer look. It dives into Availability, Performance, and Quality metrics. What’s cool is that organizations select the best for their unique production needs. Through this, you get a super accurate picture of how efficient the equipment is.
Plant Floor Metrics:
Plant floor metrics are like the superheroes of the production site. These are the key performance indicators (KPIs) measured right where the action is. Think Availability, Performance, and Quality. Keeping tabs on these metrics on the plant floor helps organizations spot spots for improvement. It’s like having a real-time dashboard to make things better on the shop floor. Also, make sure that everything runs smoothly and efficiently.
What Are the Common OEE Calculation & Monitoring Mistakes?
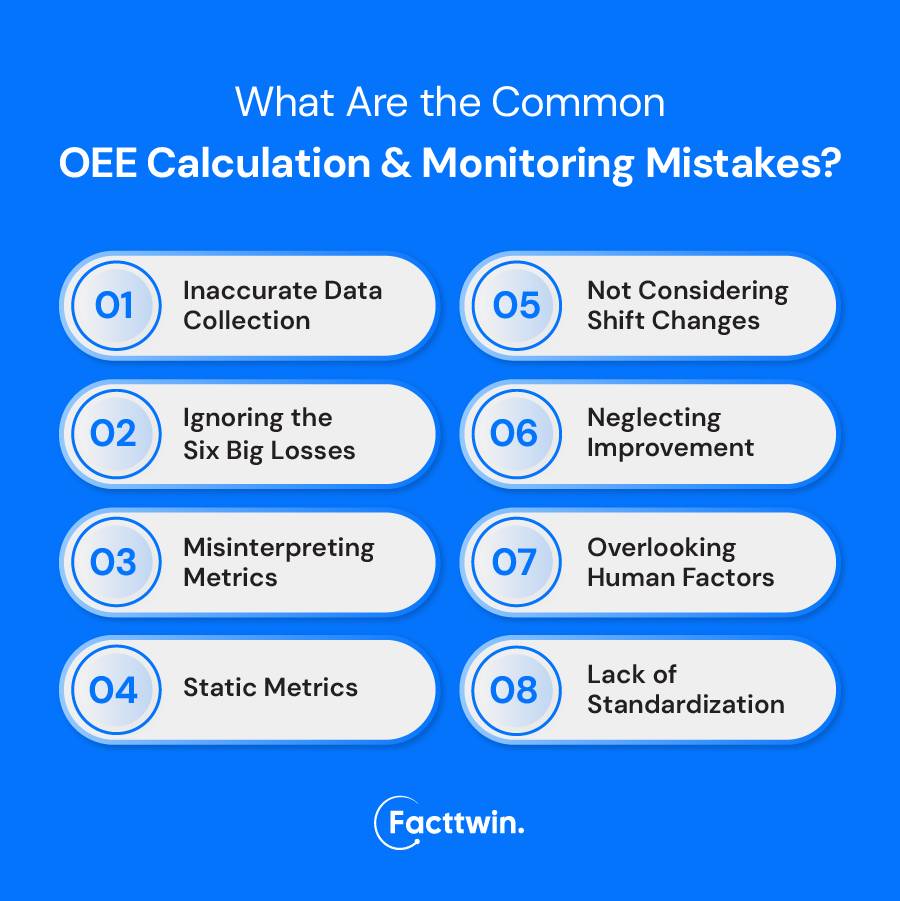
Common OEE calculation and monitoring mistakes can hinder the accuracy and effectiveness of assessing OEE in manufacturing. It is essential to identify and address these challenges. Some prevalent mistakes include:
- Inaccurate Data Collection:Relying on inaccurate or incomplete data for OEE calculations can lead to skewed results. Errors in recording downtime, production counts, or quality metrics compromise the reliability of OEE measurements.
- Ignoring the Six Big Losses:Overlooking one or more of the Six Big Losses (breakdowns, changeovers, idling, reduced speed, quality defects, start-up losses) can result in an incomplete assessment of efficiency, as these losses directly impact OEE.
- Misinterpreting Metrics:Incorrectly interpreting OEE metrics or conflating availability, performance, and quality measurements can lead to misguided conclusions and misguided efforts to improve efficiency.
- Static Metrics:Failing to adapt OEE metrics to changing production goals, product mixes, or technological advancements can result in outdated benchmarks that do not reflect the current state of the manufacturing process.
- Not Considering Shift Changes:OEE calculations may overlook the impact of shift changes on equipment efficiency. Failure to account for variations in performance during different shifts can lead to inaccurate assessments.
- Neglecting Continuous Improvement:OEE is a dynamic metric that should drive continuous improvement. Neglecting the use of OEE data as a catalyst for ongoing enhancements in processes, maintenance, and training undermines its potential impact on overall operational excellence.
- Overlooking Human Factors:Human factors, such as operator skills, training, and motivation, play a significant role in OEE. Ignoring the human element can result in missed opportunities to optimize equipment performance.
- Lack of Standardization:Inconsistent methodologies for calculating OEE across different shifts, lines, or plants can hinder accurate benchmarking and make it challenging to identify best practices.
What is Availability? How to Calculate Availability?
Availability in OEE refers to the percentage of time equipment is available for production. It is calculated using the formula:
Availability = Planned Production Time/Operating Time × 100%
Operating time represents the actual time the equipment is in production, while Planned Production Time is the total time the equipment should be available. A higher availability percentage indicates better equipment utilization.
What is Performance? How to Calculate Performance?
Performance in OEE assesses the speed and efficiency of equipment during production. The Performance metric is calculated as:
Performance = Actual Cycle Time /Ideal Cycle Time × 100%
Ideal Cycle Time is the fastest time the equipment can produce a unit, while Actual Cycle Time is the time it takes in real-world production. A higher performance percentage means optimal equipment speed and efficiency.
How to Use Overall Equipment Effectiveness (OEE) to Measure Manufacturing Productivity
OEE in manufacturing productivity involves a strategic and systematic approach. Let’s check out in what cases you can use OEE to measure manufacturing productivity.
Establish Clear Objectives:
Clearly define your manufacturing objectives and align them with broader business goals. Determine specific productivity targets and performance indicators that OEE will help measure.
Implement OEE Tracking System:
Set up a robust system to track OEE metrics. This involves collecting real-time data on Availability, Performance, and Quality. Employ sensors, automation, and data collection tools to ensure accurate and timely information.
Identify Key Performance Indicators (KPIs):
Identify relevant KPIs that align with OEE metrics. These may include production output, machine utilization, and quality rates. Establish benchmarks and targets for these KPIs based on industry standards or internal goals.
Analyze OEE Data:
Dive into the nitty-gritty of your OEE data regularly. Hunt for patterns, spot trends, and zero in on areas that could use a boost. When downtime hits or performance takes a dip, don’t just scratch the surface – let the Availability, Performance, and Quality details of your OEE be your detective toolkit. It’s not just about numbers; it’s about unveiling the story behind them, helping you fine-tune your processes and keep everything running like a well-oiled machine.
Address Six Big Losses:
Prioritize addressing the Six Big Losses—breakdowns, changeovers, idling, reduced speed, quality defects, and start-up losses. Mitigating these losses directly contributes to enhanced OEE and improved manufacturing productivity.
Embrace Continuous Improvement:
Create an environment that thrives on getting better every day, using the insights gleaned from OEE data. Team up, brainstorm, and put in place measures that boost efficiency. Regularly give your processes a tune-up to keep performance at its best.
Supercharge Preventive Maintenance:
Let OEE data be your guide for scheduling and fine-tuning preventive maintenance activities. By nipping equipment issues in the bud, you’re not just preventing surprise downtime but ensuring a continuous flow of operation and a bump in productivity.
Empower Your Crew:
It’s all about the people’s power. Provide training and give your team the tools to understand and contribute to OEE goals. Engaged and knowledgeable employees aren’t just workers; they’re champions in spotting improvement opportunities and rolling out best practices. Together, let’s rev up efficiency!
Benchmark and Compare:
Benchmark OEE metrics against industry standards and compare performance across different shifts, lines, or plants. This helps identify best practices, areas for standardization, and opportunities for cross-functional learning.
Integrate OEE into Decision-Making:
Incorporate OEE metrics into decision-making processes at all levels of the organization. Utilize OEE insights to inform strategic decisions related to production planning, resource allocation, and technology investments.
Organizations can harness the power of OEE to measure manufacturing productivity by following these considerations.
FAQs – Equipment Effectiveness (OEE) in Manufacturing
What is the OEE formula?
The OEE formula is a percentage calculated by multiplying Availability, Performance, and Quality metrics:
OEE = Availability × Performance × Quality.
What is OEE in manufacturing?
OEE in manufacturing is a key metric that assesses the overall efficiency of equipment, considering Availability, Performance, and Quality factors.
What does 85% OEE mean?
An 85% OEE indicates that the equipment is operating at 85% of its optimal efficiency, factoring in availability, performance, and quality metrics.
Conclusion
OEE is a crucial metric in production manufacturing. It evaluates efficiency through Availability, Performance, and Quality. It optimizes processes and enhances operational efficiency so that informed decisions can be made
The Six Big Losses highlight areas for improvement. OEE benefits include boosted productivity and streamlined decision-making. The formula,
OEE = Availability × Performance × Quality encapsulates equipment efficiency.
Simple and preferred OEE calculations simplify evaluation. Pitfalls like inaccurate data collection must be avoided. Utilizing OEE for productivity involves clear objectives, analysis, loss addressing, and empowering the workforce. Integration into decision-making ensures continuous improvement and sustainable success in manufacturing.